Blown-in (aka blow-in) insulation is loose fill material installed using a truck mounted or portable machine and blown into the attic through a hose. Blown-in insulation is used for new construction and retrofitting existing attics with additional insulation. R-values for blown-in are determined by the material, installed/settled depth, and density. See below for Homeowner vs. Installer benefits for cellulose and fiberglass.
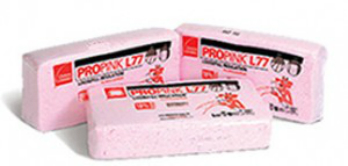
Free Estimates
Call 623-313-3194 for a free phone or in-home estimate for your Blown-in insulation and Home Efficiency needs.
- Statewide Arizona service
- Experienced knowledgeable installers
- Easy to understand proposals
- Licensed (ROC 255064), Bonded, and Insured
Retrofitting with Blown-in Insulation
Retrofitting is a simple cost effective way to dramatically improve your homes efficiency. Retrofitting is adding blown-in insulation to an existing attic. Blown-in insulation is the best way to increase an attic’s R-value. An older home may be severely deficient and a new home my have been cheated by the builder. Adding an additional layer of insulation to your homes attic is easy and effective way to increase your home’s efficiency. We recommend adding a topper to the existing insulation to achieve the desired final R-Value. Removal of the existing insulation is rarely necessary; only when contaminated by smoke, hazardous materials, rodent droppings, bird debris, insects, or mold do we recommend extraction.
New Construction
Blown-in Cellulose and Fiberglass are excellent products for new construction. Blown-in insulation may be used in attics with ample room for an installer. Typically attics with a pitch of 3:12 or greater will provide enough room for an installer to crawl through the trusses. Often fiberglass batts are used in areas with limited access. The insulation is installed directly onto the top of the ceiling drywall. R-value (higher the better) is recommended to be R-30 at minimum. EcoSystems recommends R-38 for new construction, but check the available maps for your local area. Be sure to install air barriers over wall cavities to reduce the material needed as well as provide a tighter envelope.
Cellulose vs. Fiberglass
Blown-in Cellulose Homeowner Benefits
- Higher R-Value per inch. Cellulose has an R-value of 3.5 – 3.7 per inch, where fiberglass has around 2.1-2.7 R per inch.
- Cellulose retains more of its R-Value through a wider range of temperatures compared to fiberglass. When tested at 110⁰ cellulose will retain 97% of the listed R-Value while fiberglass loses 12% or more. At sub-zero temps the R-Value of cellulose improves where fiberglass will lose half of its stated R-value.
- Cellulose has 38% better air infiltration than fiberglass. Cellulose forms a dense continuous mat of insulation in your attic. This keeps the air from moving within the insulation and from penetrations between the air-conditioned space and the attic.
- Cellulose is more difficult to cheat than fiberglass. Both cellulose and fiberglass need to be installed at the correct depth and density to achieve the intended R-value. Poorly installed fiberglass will keep an “over-fluffed” thickness, where “over-fluffed” cellulose tends to deflate quickly revealing a poor installation. Unscrupulous fiberglass installers will often use this condition to cheat customers out of material and R-Value.
- Cellulose performs better when filling small cracks and crevices. Cellulose will get inbetween gaps in fiberglass batts where blown-in fiberglass tends to bridge over gaps.
- Cellulose’s density is great to reduce sound from the outside.
Blown-in Fiberglass Homeowner Benefits
- Brand name recognition. Owens Corning “Pink Panther” and other fiberglass manufactures are household names.
- Dust from fiberglass is easier to mitigate during the install process.
- It’s pretty. Modern blown-in fiberglass resembles snow.
Blown-in Cellulose Installer Benefits
- Local source provides consistent deliveries.
- Cellulose produces much less static than fiberglass.
- Cellulose resists blowing when installed, fiberglass tends to blow around, stick to the attic ceiling, and drift. Cellulose is easier to keep out of bird blocks and air conditioner condensate pans.
- More consistent pricing from cellulose manufacturers than fiberglass. The manufacture of fiberglass is 80% more energy intensive than cellulose.
Blown-in Fiberglass Installer Benefits.
- Less material handling. 2.5 to 3 times the amount of square footage of fiberglass can be loaded onto a truck or warehouse compared to cellulose. Where a typical house would take 50 bags of cellulose, only 16-19 bags of fiberglass would be needed.
- Fiberglass won’t settle (even if cheated, huge negative for homeowner if installed incorrectly).
- Fiberglass tends to install more quickly than cellulose.
- Fiberglass manufacturers provide better marketing tools and resources.
- Less trash is produce from empty bags. Fewer bags are used with fiberglass.
- Fiberglass requires less crawling in the attic because it will blow further than cellulose.
- Less attic dust, fewer dust masks, and improved attic visibility.
- Customers like the snow-like look of modern fiberglass.
- Fiberglass is easier on installation equipment. Seals, blowers, and motors last longer when fiberglass is used. Equipment also stays cleaner.